Button snaps are widely used in the garment, packaging, and bag manufacturing industries due to their secure and convenient fastening capabilities.
For industrial manufacturers, knowing how to attach button snaps efficiently is crucial for maintaining high production standards.
In this guide, we will focus on the advantages of using fully automatic snap button machines and provide a detailed overview of the attachment process. This method ensures precision, efficiency, and consistency, significantly improving production output and reducing costs.
What are Button Snaps?
A snap button, also known as a press stud or popper, is a type of fastener used in garments, accessories, and various other applications.
Snap buttons consist of two interlocking discs, typically made of metal or plastic, which are used to fasten two pieces of fabric or material together.
When pressed together, the discs “snap” into place, creating a secure closure that can be easily opened and closed.
The Different Types of Snap Buttons
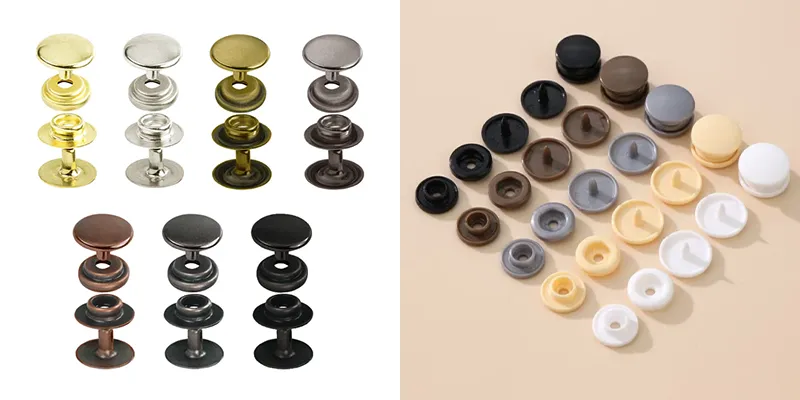
Snap buttons can be categorized based on the material they are made from metal and plastic. Each type has its unique characteristics and is suited for different applications.
Feature | Metal Snap Buttons | Plastic Snap Buttons |
---|---|---|
Durability | High | Moderate |
Strength | Very strong | Moderate |
Weight | Heavier | Lightweight |
Aesthetic Options | Limited finishes (nickel, brass) | Wide range of colors and designs |
Cost | Generally more expensive | More cost-effective |
Applications | Heavy-duty, professional items | Lightweight, casual items |
How to Attach Button Snaps?
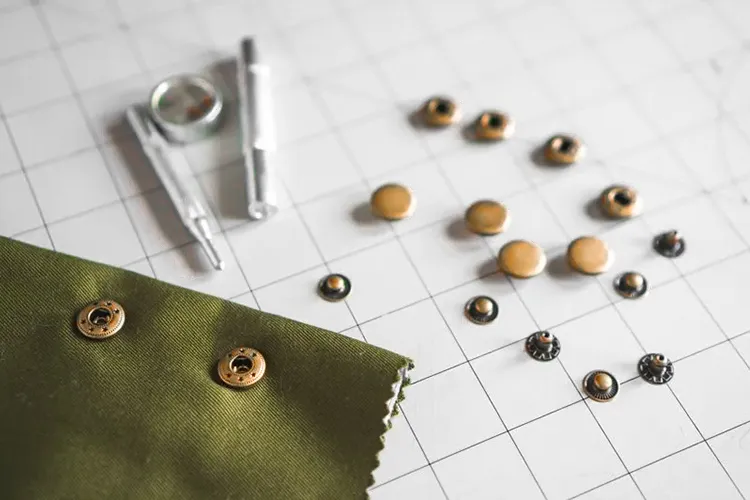
Manually Hammer to Attach Button Snaps
For many years, the installation of snap buttons has relied on workers manually hammering them into place. This traditional method of installation has several significant drawbacks:
Low Efficiency: The manual installation process of snap buttons is time-consuming and labor-intensive. Each snap needs to be individually hammered into place, which severely limits production efficiency, especially in high-volume manufacturing environments.
Inconsistent Accuracy: Ensuring consistent accuracy with manual installation is challenging. Human factors can cause variations in the placement and pressure applied to each snap, leading to inconsistencies and potential misalignments in the finished product.
Safety Hazards: Manual hammering poses safety risks to workers. The repetitive motion and force required can lead to physical strain and injuries over time. Additionally, the use of hammers increases the risk of accidental injuries, such as hitting fingers or damaging the material.
Quality Control Issues: Due to the variability in manual installation, maintaining a uniform quality standard is difficult. Misaligned or improperly attached snaps can result in defective products, affecting the final product’s overall quality and reliability.
Increased Labor Costs: Relying on manual labor for snap button installation increases labor costs. The process is slow and requires more workers to meet production demands, which can be costly for manufacturers.
By contrast, fully automatic snap button-pressing machines address these issues by enhancing efficiency, ensuring consistent accuracy, improving safety, maintaining quality control, and reducing labor costs.
These machines are an invaluable asset for industrial applications, providing a reliable and efficient solution for snap button installation.
Using an Automatic Snap Button Machine to Attach Button Snaps
Step 1: Prepare the Fabric
Lay the fabric flat on a clean, stable surface. Use a marking tool (fabric chalk or pencil) to mark the exact position where the snap will be placed. Accurate marking ensures correct alignment of the snaps.
Step 2: Load the Snap Button Machine
Load the snap button components into the machine. Follow the machine’s manual for specific loading instructions. Typically, the machine will have designated slots or trays for each component (cap, socket, stud, and post).
Step 3: Adjust Machine Settings
Adjust the machine settings according to the fabric’s thickness and type. This may include setting the pressure, height, and other parameters to ensure a secure attachment. Proper adjustment is key to achieving a professional finish.
Step 4: Position the Fabric
Place the marked fabric under the machine’s attachment area. Ensure the marked spot aligns with the machine’s attachment mechanism.
Step 5: Attach the Cap and Socket
Activate the machine to attach the cap and socket to one side of the fabric. The machine will automatically press the cap and socket together, securing them in place. Verify that the components are firmly attached and properly aligned.
Step 6: Attach the Stud and Post
Repeat the process for the stud and post on the opposite side of the fabric. Ensure that the components are securely attached and aligned with the cap and socket. The machine’s automatic operation will handle the pressing and securing.
Advantages of Using an Automatic Snap Button Pressing Machine
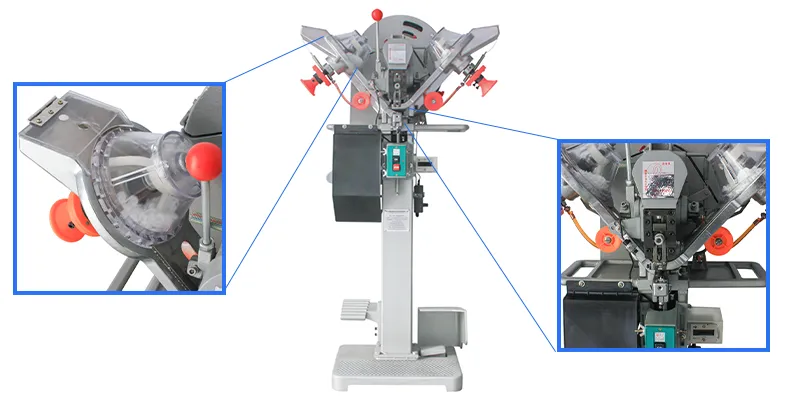
Increased Efficiency: Automatic machines can handle large volumes of snap attachments quickly, reducing the time required compared to manual methods.
Consistency and Precision: Automatic machines ensure each snap is attached with precise alignment and consistent pressure, resulting in uniform quality.
Cost Reduction: By automating the process, labor costs are reduced, and material waste is minimized, leading to lower overall production costs.
Versatility: These machines can be adjusted for various snap sizes and fabric thicknesses, making them suitable for diverse applications.
Tips for Successful Snap Attachment
- Practice on Scrap Fabric: Before attaching snaps to your final product, practice on scrap fabric to get a feel for the machine and ensure proper settings.
- Maintain Your Machine: Regularly clean and maintain your snap button machine to keep it in optimal working condition. Follow the manufacturer’s maintenance guidelines.
- Use Quality Snaps: Invest in high-quality snap button components to ensure durability and a secure hold. Cheap snaps may not provide reliable performance.
- Check Alignment: Always double-check the alignment of the snaps before pressing. Misaligned snaps can result in a poor finish and reduced functionality.
- Follow Safety Precautions: When operating the snap button machine, follow all safety precautions provided by the manufacturer to prevent accidents and injuries.
Common Mistakes to Avoid
- Incorrect Fabric Placement: Ensure the fabric is positioned correctly under the machine to avoid misaligned snaps.
- Insufficient Pressure Adjustment: Adjust the machine’s pressure settings based on the fabric thickness to ensure a secure attachment.
- Using Low-Quality Snaps: Low-quality snaps may break or fail to hold securely. Always use high-quality components.
- Neglecting Machine Maintenance: Regular maintenance is crucial for the machine’s longevity and performance. Neglecting maintenance can lead to malfunctions.
Conclusion
Using a fully automatic snap button pressing machine is an efficient and precise method suitable for industrial applications. By following the step-by-step guide and implementing the tips provided, manufacturers can achieve professional and consistent results.
Investing in high-quality snap button machines and components will ensure durability and reliability in finished products, enhancing production capabilities and meeting high standards and customer expectations.