In the textile industry, spreading machines are vital for efficiently handling and distributing fabrics across a workspace. These machines are used to layer fabric evenly before further processes like cutting or stitching. By using a spreading machine, manufacturers can improve productivity, maintain fabric quality, and reduce operational costs. In this article, we’ll explore the various types of spreading machines, their benefits, and how to select the right one for your needs.
What is a Spreading Machine?
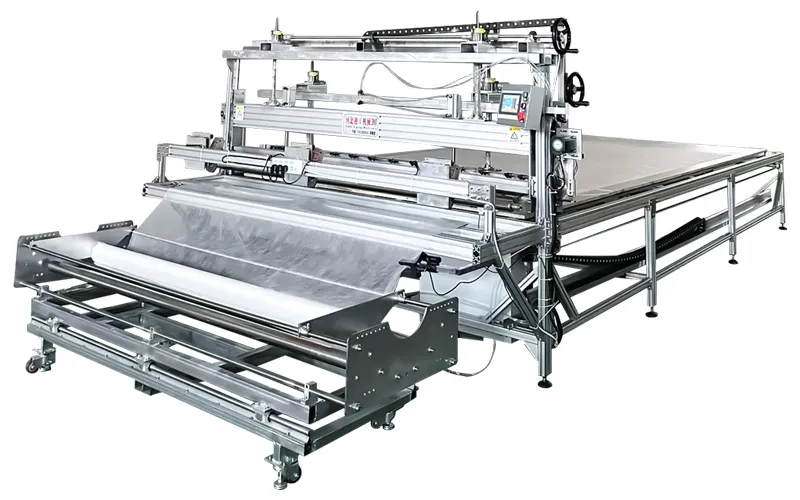
Definition and Role in Textile Manufacturing
A spreading machine is a specialized piece of equipment used to evenly distribute fabric across a flat surface. It rolls out, spreads, and arranges fabric layers in a controlled manner. This is especially important when dealing with large rolls of fabric that need to be precisely aligned for cutting, pattern marking, or stitching.
In textile manufacturing, precision and consistency are crucial, and spreading machines play a major role in ensuring these factors. They allow manufacturers to work more quickly and with greater accuracy, improving overall production efficiency.
How Spreading Machines Impact Fabric Handling
Spreading machines handle fabric with care, preventing stretching or warping. By maintaining uniformity in fabric tension, they ensure that every layer of fabric is consistently placed. This uniformity is crucial for ensuring that the final products, such as garments or quilts, meet quality standards.
Key Types of Spreading Machines
Overview of Different Categories of Spreading Machines
There are several types of spreading machines, each designed for specific tasks and fabric types. The key types include:
- Manual Spreading Machines
- Automatic Spreading Machines
- Semi-Automatic Spreading Machines
Manual Spreading Machines
Manual spreading machines require operators to control the fabric’s movement by hand. While they are slower than automated versions, they are suitable for smaller production runs and specific fabrics that require extra care. Manual machines are more affordable and are ideal for businesses with limited budgets or smaller-scale operations.
Operation and Benefits
Manual spreading machines are typically operated using foot pedals or hand cranks. They give operators full control over the fabric, which can be beneficial for delicate or specialty materials. The main advantage of manual machines is the lower upfront cost, though they do require more human labor and time compared to automatic machines.
Automatic Spreading Machines
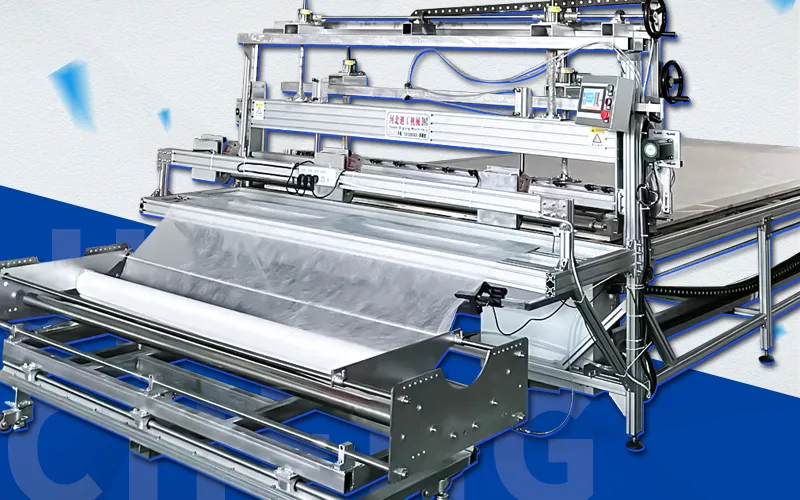
Automatic spreading machines are designed for high-volume textile manufacturing. They operate with minimal human input, automatically spreading the fabric across a surface and aligning it perfectly. These machines are faster and more accurate than manual machines, making them ideal for large-scale operations.
Features and Advantages
Automatic machines feature advanced sensors and control systems that can adjust the fabric tension, speed, and alignment automatically. This reduces the risk of human error and increases efficiency. Moreover, automatic spreading machines can handle larger rolls of fabric, making them a better choice for high-production environments.
Semi-Automatic Spreading Machines

Semi-automatic machines combine elements of both manual and automatic spreading. These machines require an operator to load the fabric, but they automate the spreading process. This strikes a balance between the labor of manual machines and the speed of automatic machines.
Efficiency and Application
Semi-automatic machines are perfect for medium-sized businesses that need faster production but cannot justify the high cost of fully automatic machines. They are more efficient than manual machines, yet still allow for operator control when needed.
Advantages of Using Spreading Machines
Why Spreading Machines Are Essential for Textile Production
Spreading machines provide several key benefits to textile manufacturers:
- Increased Efficiency – These machines allow for fast and uniform fabric distribution, reducing production time.
- Enhanced Precision – Spreading machines minimize human error and ensure fabric layers are aligned perfectly.
- Cost Savings – Though there is an initial investment, spreading machines save time and labor costs in the long term.
- Improved Fabric Quality – By reducing handling errors, spreading machines help maintain the integrity of fabrics.
Time Efficiency
Spreading machines can work much faster than manual methods, significantly reducing the time it takes to prepare fabric for further processing. For instance, while manual labor might take hours to layer fabric, a spreading machine can do it in a fraction of the time.
Quality Consistency
The precision of spreading machines ensures that each layer of fabric is consistent, which is vital for products like clothing or upholstery. Any inconsistencies in fabric layers can lead to defects in the final product, which spreading machines help avoid.
Cost Effectiveness
Although the initial investment may be high, spreading machines save money over time by reducing labor costs and increasing production output. Additionally, the quality improvements reduce the need for rework and minimize fabric waste.
Choosing the Right Spreading Machine
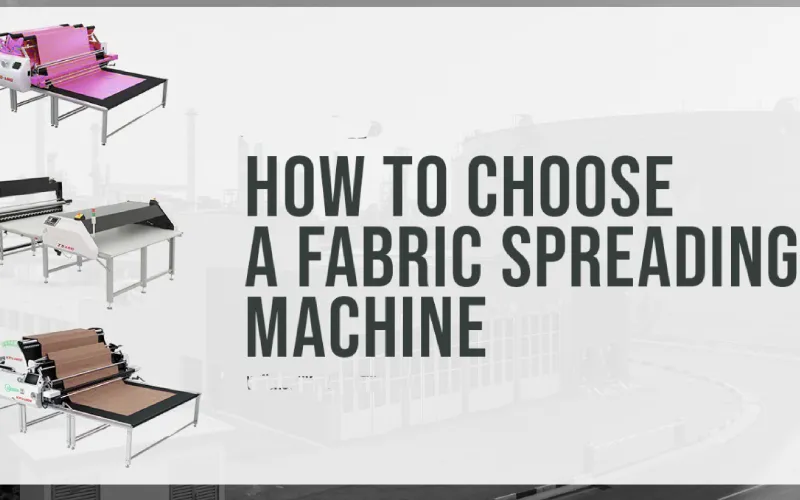
Factors to Consider When Selecting a Spreading Machine
When choosing a spreading machine, it’s essential to consider several factors to ensure you select the right machine for your needs.
Fabric Type and Thickness
Different fabrics require different spreading techniques. For instance, lightweight fabrics like silk may need a more delicate spreading machine, while heavy fabrics like denim may require machines with more robust motors and systems.
Production Volume
If you have a high production volume, an automatic or semi-automatic machine would be the best choice, as they can handle larger quantities of fabric more efficiently. Manual machines are better suited for smaller batches or niche products.
Machine Speed and Output
The speed of the spreading machine is another critical factor. For businesses with high throughput requirements, machines that can spread fabric at higher speeds are essential. However, for more delicate tasks, slower machines may be more appropriate to ensure quality control.
Maintenance and Care for Spreading Machines
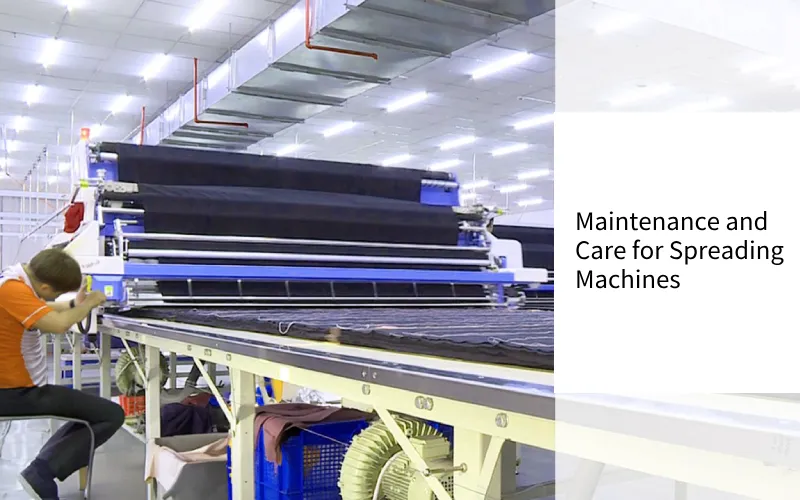
Keeping Your Spreading Machine in Top Condition
To ensure longevity and optimal performance, regular maintenance is necessary.
Regular Inspections
Inspecting the machine periodically ensures that all components are functioning correctly. Look for issues like fabric misalignment, motor performance, and sensor calibration.
Lubrication and Cleaning
Maintaining a clean and lubricated machine is essential for reducing wear and tear. Follow the manufacturer’s guidelines for routine cleaning and lubrication.
Common Issues with Spreading Machines
Troubleshooting Common Problems and Solutions
Despite their efficiency, spreading machines can encounter problems. Here are a few common issues:
Fabric Jams
Fabric jams can occur if the fabric isn’t properly aligned or if the tension is too tight. Ensuring the fabric is correctly loaded and adjusting tension settings can help prevent jams.
Incorrect Fabric Alignment
If the fabric layers aren’t aligned correctly, it can result in uneven distribution. Recalibrating the machine’s sensors or manually realigning the fabric can resolve this issue.
Types of spreading machines, whether manual, semi-automatic, or automatic, offer significant advantages for fabric handling in textile production. These machines improve speed, precision, and cost-efficiency, making them essential tools for any textile manufacturer. When selecting a machine, consider factors such as fabric type, production volume, and machine speed to ensure the right fit for your operations.
FAQs about Spreading Machines
What is the difference between manual and automatic spreading machines?
Manual spreading machines require human effort for fabric alignment, while automatic machines handle all aspects of spreading independently, increasing speed and accuracy.
Can a spreading machine be used for all fabric types?
Yes, but it’s important to choose a spreading machine designed for specific fabric types. Some fabrics, like delicate silks or stretchy materials, may require specialized machines.
How often should a spreading machine be maintained?
Spreading machines should be inspected regularly, with routine maintenance performed every 3-6 months, depending on usage.
What is the cost of a spreading machine?
Costs can vary significantly depending on the type and features, with manual machines being the least expensive and automatic models being the most costly.
How does an automatic spreading machine work?
Automatic spreading machines use sensors, motors, and control systems to distribute fabric evenly and precisely, with minimal human intervention.
What are the benefits of using a spreading machine over manual methods?
Spreading machines are faster, more accurate, and more consistent than manual methods, leading to better product quality and higher production volumes.
Conclusion
Understanding the different types of spreading machines is crucial for optimizing textile production. Investing in the right machine can significantly enhance efficiency and accuracy, ultimately leading to reduced costs and higher quality in garment manufacturing.