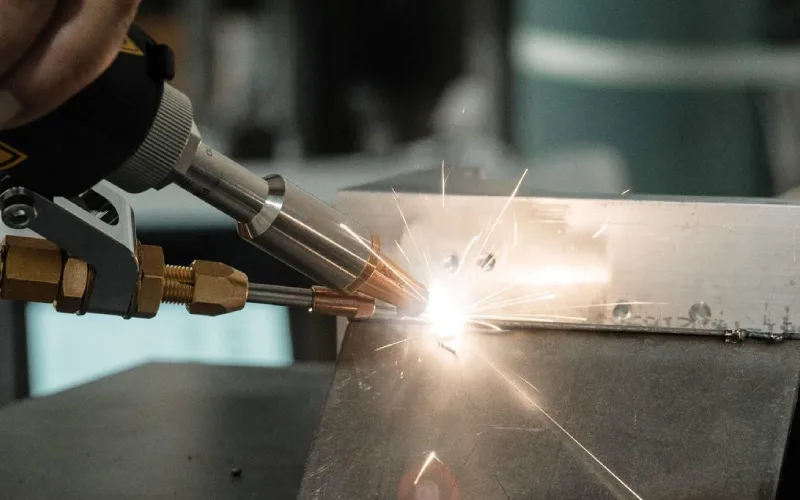
What is a Laser Welding Machine?
A laser welding machine is an advanced technological tool that utilizes focused laser beams to create strong, precise joints between materials. This technique has revolutionized the welding industry, providing numerous advantages over traditional methods such as arc welding or gas welding. With applications spanning various industries, including automotive, aerospace, electronics, and medical device manufacturing, laser welding offers unparalleled precision, speed, and flexibility.
How Laser Welding Works
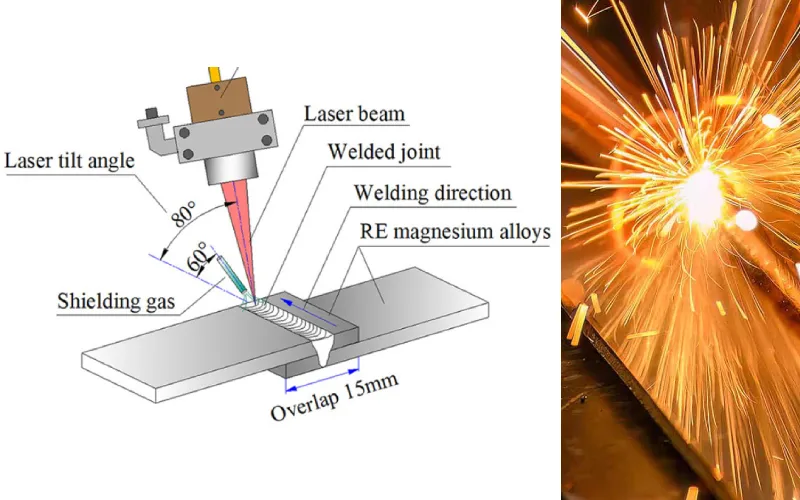
The core principle behind laser welding lies in the interaction between the laser beam and the material being welded. The process can be broken down into several key steps:
- Laser Generation: The machine generates a high-energy laser beam using different types of lasers, such as solid-state, fiber, or CO2 lasers. The choice of laser depends on the specific application and material requirements.
- Focusing the Beam: The generated laser beam is directed through optics, which focus the beam to a fine point. This concentrated energy is crucial for achieving the high temperatures needed to melt the materials.
- Melting the Material: When the focused laser beam strikes the surface of the material, it rapidly heats the area, creating a molten pool. The intensity of the laser allows for precise control over the heat input, which is vital for achieving high-quality welds.
- Cooling and Solidification: Once the laser moves away, the molten pool cools and solidifies, forming a strong metallurgical bond between the materials. The cooling rate can affect the microstructure of the weld, impacting its mechanical properties.
Types of Laser Welding Machines
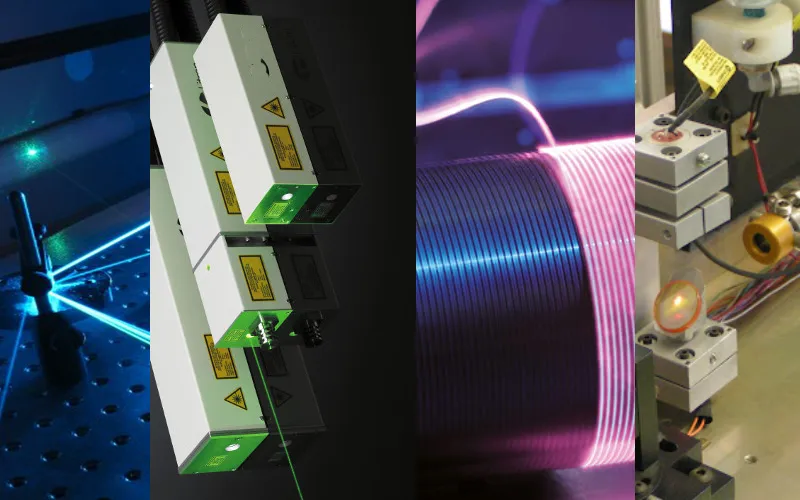
Laser welding machines can be classified based on their laser source and operational characteristics. Here are the primary types:
1. Continuous Wave Lasers
Continuous wave (CW) lasers emit a constant beam of light. They are commonly used for welding applications where consistent power is necessary. CW lasers are effective for joining thick materials and are often found in industrial environments.
2. Pulsed Lasers
Pulsed lasers deliver energy in short bursts rather than continuously. This feature allows for greater control over the heat input, making pulsed lasers ideal for welding thin or delicate materials, such as plastics and metals. The pulse duration can be adjusted to minimize heat-affected zones, reducing the risk of warping or damaging the workpiece.
3. Fiber Lasers
Fiber lasers are renowned for their efficiency and versatility. They use a doped fiber optic as the laser medium, which results in excellent beam quality and high output power. Fiber lasers are particularly effective for welding thin sheets of metal and are increasingly popular in industrial applications due to their low maintenance requirements and compact design.
4. CO2 Lasers
CO2 lasers are one of the most widely used types in manufacturing due to their ability to weld a variety of materials. They generate high-powered beams and are suitable for thicker materials. However, CO2 lasers often require more extensive cooling systems and can be more costly to operate.
Advantages of Laser Welding Machines
Laser welding machines offer a multitude of benefits that make them an attractive choice for manufacturers:
High Precision and Quality
One of the most significant advantages of laser welding is its precision. The focused laser beam allows for extremely accurate welds, minimizing defects and ensuring consistent quality. This level of precision is especially critical in industries where safety and reliability are paramount, such as aerospace and medical device manufacturing.
Speed and Efficiency
Laser welding is a fast process that can significantly increase production rates. The ability to perform quick welds reduces cycle times, allowing manufacturers to meet tight deadlines and boost overall productivity. This efficiency is particularly advantageous in high-volume production environments.
Minimal Heat Affected Zone
Laser welding generates less heat compared to traditional welding methods, resulting in a smaller heat-affected zone (HAZ). This characteristic is crucial for maintaining the integrity of the surrounding material, as it reduces the risk of warping, distortion, and other thermal damages.
Versatility
Laser welding can be applied to a wide range of materials, including metals, plastics, and ceramics. It can also accommodate various thicknesses, making it suitable for diverse applications across different industries. Additionally, laser welding can be performed in challenging environments, such as those requiring remote or automated operations.
Reduced Need for Post-Weld Treatment
Due to the high quality of laser welds and the minimal HAZ, there is often less need for post-weld treatments such as grinding or polishing. This feature can lead to cost savings and faster turnaround times for finished products.
Applications of Laser Welding Machines
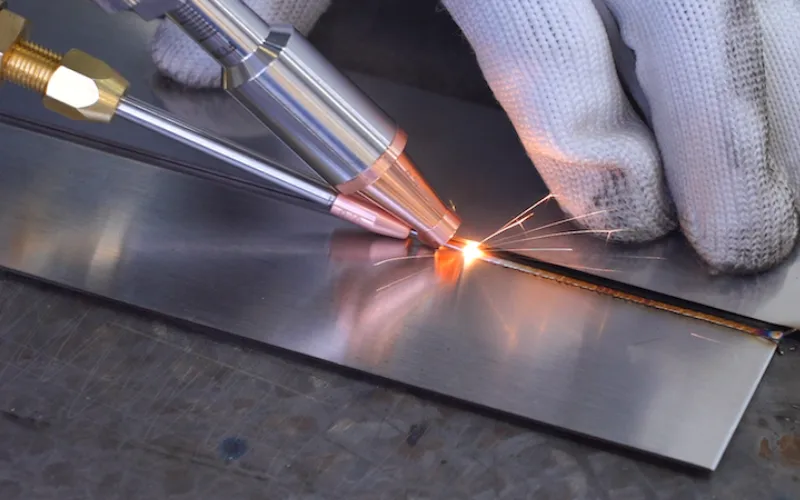
Laser welding is utilized across multiple sectors, each benefiting from its unique advantages:
Automotive Industry
In the automotive sector, laser welding is employed for joining components such as body panels, structural parts, and exhaust systems. The precision and speed of laser welding make it ideal for high-volume production, ensuring vehicles are assembled efficiently while maintaining structural integrity.
Aerospace Sector
Aerospace manufacturing requires extremely high-quality welds due to the safety-critical nature of the components involved. Laser welding is used to join lightweight materials, such as aluminum and titanium, in aircraft structures and engine parts, providing strength without adding significant weight.
Electronics Manufacturing
The electronics industry utilizes laser welding for assembling delicate components, including circuit boards and connectors. The high precision of laser welding allows for minimal thermal impact on sensitive components, ensuring reliable performance and longevity.
Medical Device Production
In the medical field, laser welding is employed to fabricate various devices, including surgical instruments and implantable devices. The cleanliness and precision of laser welds are essential in maintaining the strict hygiene and performance standards required in medical applications.
Jewelry and Watchmaking
Laser welding is increasingly used in the jewelry and watch industries for joining intricate designs and components. The precision of laser welding allows artisans to create detailed pieces with minimal visible seams, enhancing the aesthetic appeal of the final products.
Factors to Consider When Choosing a Laser Welding Machine
Selecting the right laser welding machine involves considering several critical factors:
Material Type
Different materials may require specific types of lasers for optimal results. Understanding the properties of the materials you plan to weld is essential for choosing the appropriate machine.
Welding Thickness
Consider the thickness of the materials being joined. Some machines are better suited for thin materials, while others can handle thicker sections. Assessing your welding needs will help you select a machine that meets your production requirements.
Production Volume
Your production volume will influence the type of machine you need. For high-volume production, a machine with faster welding capabilities and automated features may be necessary, while low-volume applications might benefit from a more versatile, flexible machine.
Budget
Investing in a laser welding machine involves considering the initial purchase cost, operational expenses, and potential return on investment. It’s essential to balance performance capabilities with your budget to find the best option for your business.
Maintenance Requirements
Different laser welding machines have varying maintenance needs. Consider the long-term maintenance costs and the availability of support services to ensure your investment remains operational and efficient.
Future Trends in Laser Welding Technology
As industries continue to evolve, so does laser welding technology. Some emerging trends include:
Automation and Robotics
The integration of automation and robotics in laser welding processes is becoming increasingly common. Automated systems enhance productivity and consistency while reducing human error, making them ideal for high-volume manufacturing environments.
Advanced Beam Control
Developments in laser beam control technology are allowing for even more precise and versatile welding processes. Techniques such as beam shaping and scanning can optimize the welding parameters for different materials and applications.
Hybrid Welding Techniques
Combining laser welding with other welding methods, such as arc welding, is gaining traction. Hybrid welding can capitalize on the advantages of both techniques, providing enhanced penetration, reduced distortion, and improved weld quality.
Increasing Use of Additive Manufacturing
As additive manufacturing technologies advance, laser welding is being integrated into these processes to join components or repair parts. This synergy can enhance the capabilities of 3D printing and expand the possibilities for creating complex geometries.
FAQs
How does the cost of laser welding compare to traditional welding methods?
The initial investment for a laser welding machine can be higher than traditional welding equipment due to the technology involved. However, the long-term savings from reduced labor costs, faster production times, and lower maintenance requirements can make laser welding more cost-effective in high-volume applications.
What maintenance is required for a laser welding machine?
Regular maintenance for laser welding machines typically includes cleaning the optics, checking and replacing lenses, ensuring proper alignment, and inspecting cooling systems. Scheduled maintenance is essential to keep the machine operating efficiently and to extend its lifespan.
Do parts need to be clamped together during laser welding?
Yes, parts generally need to be clamped together during laser welding to ensure proper alignment and stability throughout the welding process. Clamping helps maintain the position of the components, preventing movement that could lead to misalignment or defects in the weld.
Proper clamping is essential for achieving consistent weld quality and strength. Additionally, clamping can help control the heat distribution during welding, minimizing distortion and ensuring a strong bond between the materials. Depending on the design and requirements of the parts being welded, various clamping methods and fixtures can be used to secure the components in place effectively.
Does laser plastic welding emit smoke or off-gassing?
Yes, laser plastic welding can emit smoke and off-gassing during the process. When the laser beam melts the plastic material, it generates heat that can cause the plastic to decompose or vaporize, leading to the release of fumes. The nature and volume of these emissions depend on several factors, including the type of plastic being welded, the laser parameters, and the specific conditions of the welding environment.
To mitigate the effects of smoke and off-gassing, it is essential to have proper ventilation and fume extraction systems in place.
Conclusion
In conclusion, laser welding machines represent a significant advancement in manufacturing technology, offering unparalleled precision, speed, and versatility. With applications spanning various industries, they are essential tools for producing high-quality welded components.
By understanding the principles, advantages, and considerations involved in selecting a laser welding machine, manufacturers can enhance their production capabilities and maintain a competitive edge in today’s fast-paced market.