Laser welding is a modern and innovative technique used across various industries for its precision and efficiency. This article delves into the intricacies of laser welding, exploring its types, applications, benefits, challenges, and future prospects.
We will also provide practical user guides, expert insights, and comparisons with other welding technologies.
What is Laser Welding
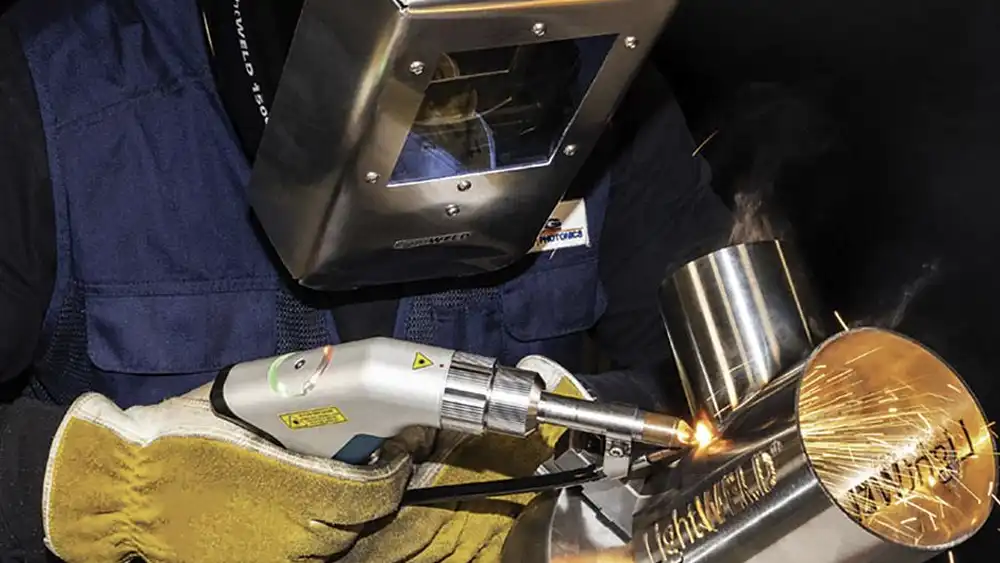
Laser welding is a technique for joining metals and some plastics using a very concentrated beam of light. This light acts like an intense heat source, melting the materials together at the seam where you want them connected. As the melted material cools, it fuses together to create a strong bond.
Here are some key points about laser welding:
- Precise: The laser beam is very narrow, which allows for highly precise welds. This is ideal for delicate applications or where minimal heat distortion is desired.
- Strong: Laser welds can be very strong, often as strong or even stronger than the base materials themselves.
- Fast: Laser welding can be a fast process, especially for thin materials.
- Versatile: Laser welding can be used on a variety of materials, including steel, stainless steel, aluminum, and some plastics.
What Is the Origin of Laser Welding?
The origin of laser welding is closely tied to the development of lasers themselves. Here’s a breakdown of its early days:
- 1917: The groundwork was laid by physicist Albert Einstein with his theory of stimulated emission, which provided the scientific foundation for lasers.
- 1960: The first functional laser was created by Theodore Maiman, opening the door to various laser applications, including welding.
- 1960s: Early experiments in laser welding began, demonstrating the potential for this technology. Researchers explored using lasers to melt and fuse metals, offering an alternative to traditional welding methods.
- 1967: A significant milestone was achieved when scientists at the Battelle Memorial Institute successfully used a laser to join two metal pieces. This marked the birth of laser welding as a viable technology.
- Since then, laser welding has evolved from experimental labs into a robust, industrial-grade process powering critical applications from aerospace to electronics.
What is Laser Welding Machine
A laser welding machine is the complete apparatus used for laser welding. It consists of several key components that work together to create a concentrated beam of light and precisely direct it onto the materials you want to weld. Here’s a breakdown of the main parts:
- Laser Source: This is the heart of the machine, generating the powerful laser beam. Common types include CO2 lasers and fiber lasers, with fiber lasers gaining popularity due to their efficiency and beam quality.
- Beam Delivery System: This intricate system of mirrors and lenses channels the laser beam from the source and focuses it into a very narrow and intense beam. Imagine a complex light pipe carefully guiding the light exactly where it needs to go.
- Beam Manipulator (Optional): In some machines, a beam manipulator like a scanner system can be used to direct the laser beam more flexibly. This allows for remote welding or integration into automated systems.
- Control System: This is the brain of the operation. It electronically controls the laser source, beam delivery system, and other parameters to ensure precise welding parameters and consistent results.
- Workstation and Shielding: The machine typically has a workstation where the parts to be welded are positioned and secured. A shielding system is often incorporated to protect the operator from the laser beam and fumes generated during the welding process.
What is Laser Welding Used For
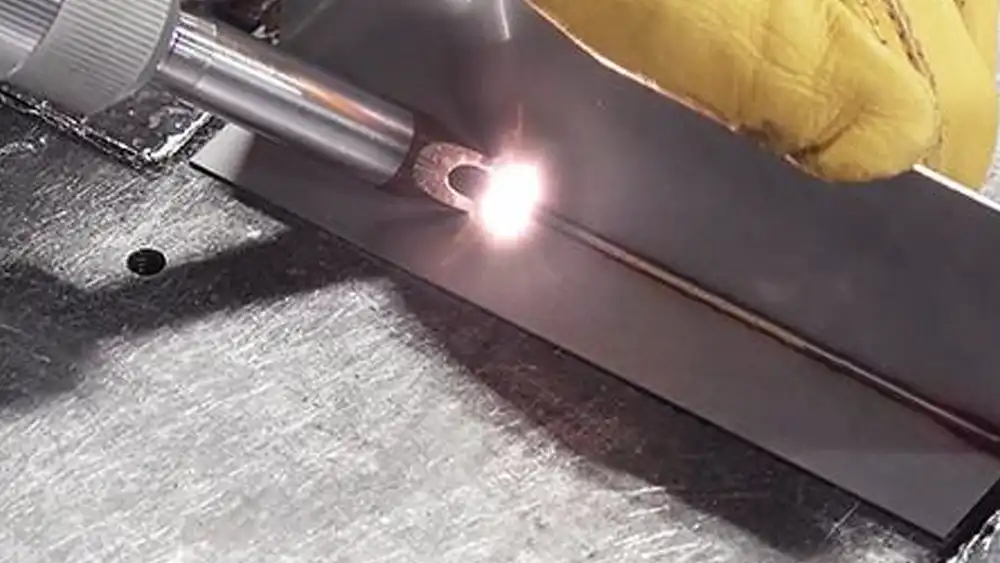
Laser welding’s precision and strength make it a go-to technique across various industries. Here are some of the common applications of laser welding:
- Automotive Industry: Joining car body parts, welding electrical components for engines and control systems.
- Aerospace Industry: Manufacturing lightweight and high-strength components for aircrafts, such as engine parts and landing gear.
- Medical Devices: Creating intricate parts for pacemakers, stents, and other delicate medical instruments.
- Consumer Electronics: Welding tiny components inside smartphones, laptops, and other electronic devices.
- Jewelry Making: Creating fine, precise welds in jewelry pieces, offering a clean and strong bond.
- Appliance Manufacturing: Joining parts for appliances like refrigerators and washing machines.
- Construction: Welding metal structures and building components.
- Eyewear Manufacturing: Creating strong and cosmetically appealing welds in eyeglass frames.
Beyond these, laser welding finds applications in numerous other sectors due to its ability to handle dissimilar metals, weld thin materials precisely, and minimize heat distortion. As laser technology continues to develop, we can expect even more innovative uses for laser welding to emerge.
How Does Laser Welding Work
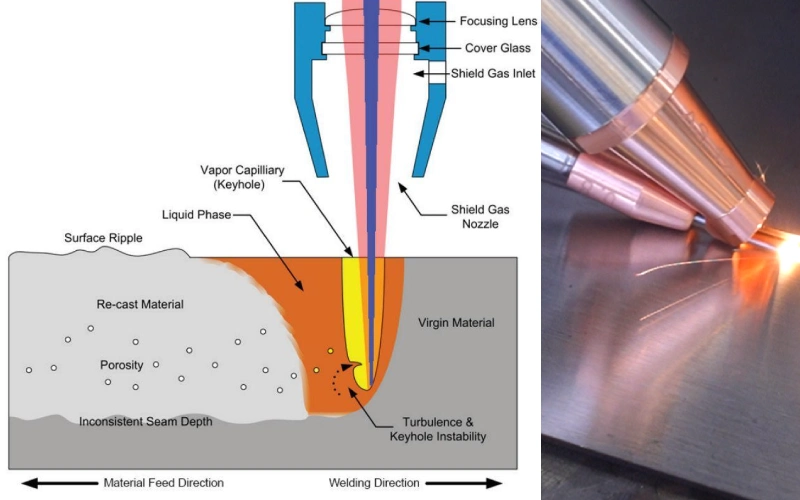
Laser welding works by harnessing the power of concentrated light to create a strong bond between materials. Here’s a step-by-step breakdown of the process:
- Generating the Laser Beam: The process starts with a laser source, which can be of different types like CO2 or fiber lasers. This source generates a beam of light with a specific wavelength.
- Beam Delivery and Focusing: The laser beam is then directed through a series of mirrors and lenses within the welding machine. This system helps to focus the beam into a very narrow and intense beam.
- Melting the Material: The highly focused laser beam hits the joint where the two pieces of material meet. The intense light energy is converted into heat upon contact with the material, causing it to melt at a localized point.
- Weld Pool Formation: The melted material forms a molten pool at the joint. In some cases, a filler metal rod may be added to the molten pool to increase the weld strength or bridge gaps between the materials.
- Solidification and Bonding: As the laser beam moves along the joint, the molten pool cools and solidifies rapidly, forming a strong metallurgical bond between the two pieces.
There are two main modes of laser welding depending on the power density of the laser beam:
- Conduction Limited Welding: In this mode, the laser beam melts the material primarily through heat conduction. This is suitable for thinner materials where deep penetration is not required.
- Keyhole Welding: With higher power densities, the laser beam creates a deep vapor cavity within the molten pool, called a keyhole. This allows for deeper weld penetration, making it ideal for thicker materials.
Laser welding offers a precise and controlled way to join materials compared to traditional welding methods. The concentrated heat source minimizes distortion in the surrounding area and allows for high-quality welds.
What Is the Process of Laser Welding
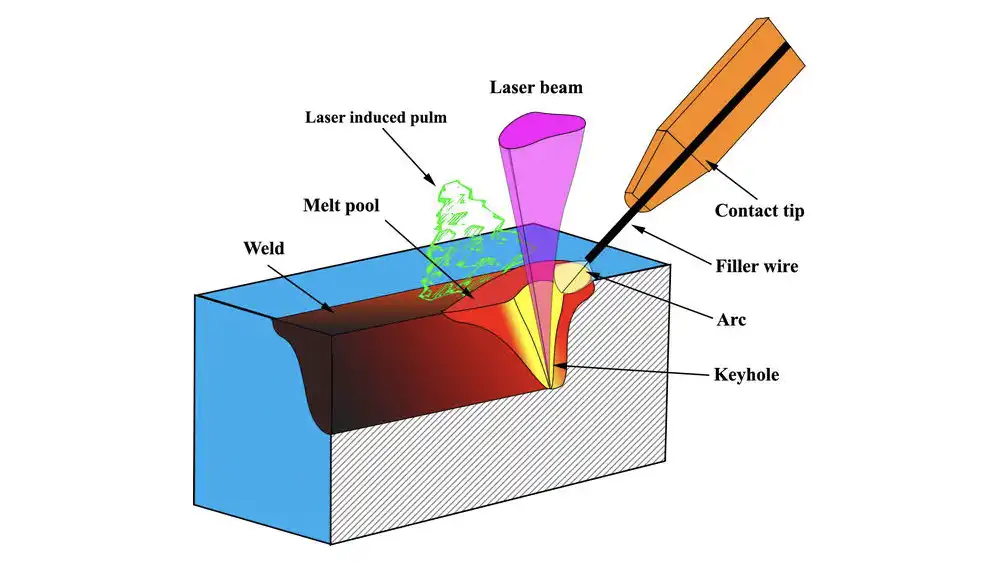
The process of laser welding involves a fascinating interplay between light and metal to create a strong bond.
Here’s a detailed breakdown of the steps involved:
- Power Up: The process starts with the laser source, which can be a CO2, fiber, or another type of laser, depending on the application. This source generates a beam of light with a specific wavelength, ready to be directed and focused.
- Beam Highway: The laser beam doesn’t travel straight to the weld site. Instead, it takes a guided tour through a series of mirrors and lenses within the welding machine. This intricate system acts like a beam highway, carefully directing and focusing the light into a very narrow and intense beam. Imagine a spotlight compared to a laser pointer – that’s the level of concentration we’re aiming for.
- Heating Up the Joint: The highly focused laser beam reaches its destination – the joint where the two pieces of material meet. Upon contact, the intense light energy gets converted into heat. This heat is highly localized, meaning it only affects a tiny area at the point of contact, minimizing heat distortion in the surrounding material.
- Molten Metal Pool: As the heat intensifies, the material at the joint starts to melt, forming a molten pool. This molten pool acts like a mini-crucible containing the melted metal. In some cases, if the desired weld is thicker or requires additional material, a filler metal rod can be introduced into the molten pool. This filler metal melts and mixes with the base metal, further strengthening the weld.
- Solidification and the Bond: The laser beam doesn’t stay in one place. It travels along the joint, continuously melting the material in its path. As the laser beam moves on, the molten pool behind it cools rapidly and solidifies. This rapid solidification creates a strong metallurgical bond between the two pieces of material, essentially fusing them together.
Here’s an interesting point to consider: Depending on the power density of the laser beam, we can have two main modes of laser welding:
- Conduction Limited Welding: This mode is suitable for thinner materials. Here, the laser beam melts the material primarily through heat conduction from the focused beam. The heat doesn’t reach a high enough intensity to create a deep vapor cavity.
- Keyhole Welding: When dealing with thicker materials, we need a deeper weld penetration. This is achieved through keyhole welding. With a higher power density, the laser beam creates a deep vapor cavity within the molten pool, called a keyhole. This keyhole allows the laser beam to penetrate deeper into the material, resulting in a stronger weld for thicker materials.
The laser welding process offers a high degree of precision and control compared to traditional welding methods. The concentrated heat source minimizes warping and distortion in the surrounding area, leading to high-quality and strong welds.
What Are the Different Types of Laser Welding?
The world of laser welding offers a variety of techniques to tackle different welding challenges. Here’s a breakdown of some common types of laser welding:
By Power Delivery and Weld Formation:
- Conduction Welding: This method uses the lowest power density among laser welding techniques. The heat from the laser beam primarily melts the material through conduction, suitable for joining thin sheets or materials with high thermal conductivity.
- Deep Penetration Welding: As the name suggests, this technique utilizes high laser power to achieve deep weld penetration. It’s ideal for thicker materials and often uses a keyhole welding mode (explained below) to achieve the depth required.
By Beam Delivery and Weld Appearance:
- Laser Spot Welding: This technique uses a focused laser beam to create small, localized welds. It’s perfect for joining tiny components or applications where minimal heat impact is desired.
- Laser Seam Welding: This method creates continuous welds by moving the laser beam along the seam where the two pieces meet. It’s widely used in applications requiring long, strong welds.
By Additional Processes:
- Remote Laser Welding: This technique uses a scanner system to deliver the laser beam through a fiber optic cable. This allows for more flexibility in reaching awkward weld locations or integrating the welding process into automated systems.
Special Techniques:
- Keyhole Welding: This mode is used within deep penetration welding and relies on a high-power density laser beam to create a vapor cavity (keyhole) within the molten metal pool. This keyhole allows for deeper weld penetration compared to conduction welding.
Other Factors:
- Laser Source: Different types of lasers are used in welding, with fiber lasers being increasingly popular due to their efficiency and beam quality. CO2 lasers are another common type.
The choice of laser welding technique depends on several factors, including the material thickness, desired weld strength and depth, and the specific application requirements.
Comparing Laser Welding to Other Methods
Feature | Laser Welding | TIG Welding | MIG Welding |
---|---|---|---|
Heat Input | Low & Focused | High | Moderate |
Speed | Fast | Slower | Moderate |
Precision | Very High | High | Moderate |
Automation | Easily Automated | Difficult | Possible |
Setup Cost | High | Low | Medium |
Material Suitability | Broad | Broad | Broad |
Laser welding is the top choice where precision, automation, and material integrity are crucial.
FAQ
1. What materials can be laser welded?
Laser welding is suitable for a wide range of metals, including stainless steel, carbon steel, aluminum, titanium, and even dissimilar metals like copper and nickel alloys. It can also be used for some plastics, depending on the laser type and setup.
2. Is laser welding better than traditional welding methods?
It depends on the application. Laser welding offers higher precision, less heat distortion, and faster processing times—especially for thin or delicate materials. However, it has a higher initial cost and may require more precise joint preparation.
3. How deep can a laser weld penetrate?
The depth of a laser weld varies based on the power of the laser and the material type. In keyhole mode, high-power lasers can achieve weld depths of up to 10mm or more in metals like steel, while lower-power systems are ideal for thin materials.
4. Is laser welding safe?
Yes, when proper safety protocols are followed. Operators must wear protective eyewear and use shielding enclosures or barriers to prevent exposure to the laser beam. Fume extraction systems are also recommended in industrial settings.
5. Can laser welding be automated?
Absolutely. One of the biggest advantages of laser welding is its compatibility with automation. It integrates easily into robotic systems, CNC machines, and production lines, making it ideal for high-precision, high-volume manufacturing.
Conclusion
Laser welding has revolutionized metal fabrication by offering a precise and powerful way to join materials. It utilizes a concentrated beam of light to create strong, clean welds with minimal heat distortion. From its scientific origins to its diverse applications across industries, laser welding has transformed how we connect and build.
Whether you’re a seasoned welder or just starting to explore joining methods, understanding laser welding opens doors to new possibilities in your projects. As technology continues to advance, laser welding is poised to play an even greater role in shaping the future of fabrication.
Ready to Explore Laser Welding for Yourself?
If you’re interested in incorporating laser welding into your projects, obtaining a quote for a laser welding machine is a great next step. Welding equipment suppliers can help you find the right machine for your specific needs and budget. They can guide you through the various factors to consider, such as:
- The type of materials you’ll be welding
- The thickness of the materials
- The desired weld depth and strength
- Your budget
With the right laser welding machine, you can unlock a new level of precision and control in your fabrication projects. Let laser welding illuminate the possibilities in your metalworking endeavors!