Laser welding has become one of the most sought-after joining techniques, thanks to its precision and impressive strength. But how strong is laser welding, really?
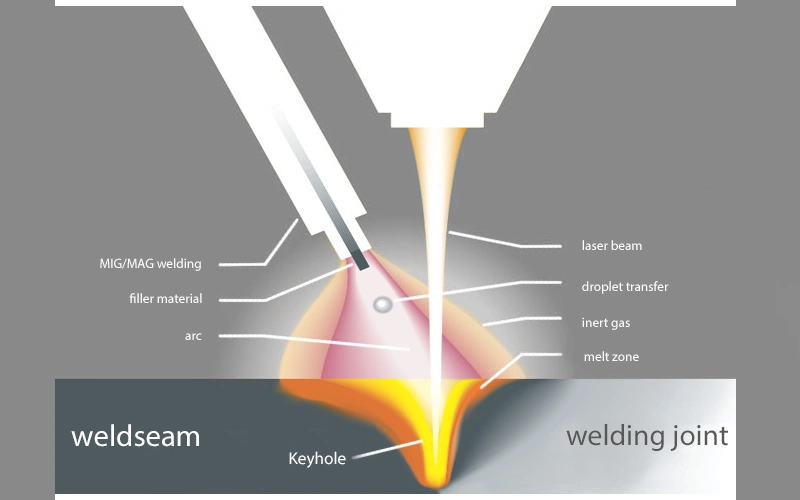
As someone who’s either curious about advanced manufacturing or actively working with welding technology, this guide will take you through everything you need to know about the topic. Let’s dive deep into the mechanics, applications, and strength of laser welding.
What Is Laser Welding?
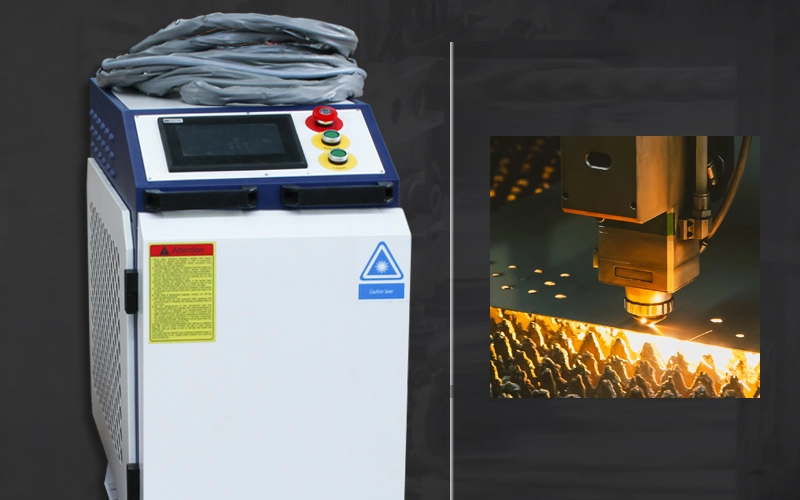
Laser welding is a high-precision technique that uses a focused laser beam to join materials, typically metals or thermoplastics. When the beam strikes the surface, it heats and melts the material, creating a seamless joint as it cools. You might think of it as a modern upgrade to traditional welding methods like MIG, TIG, or arc welding.
If you’ve ever wondered why laser welding has gained such popularity, the answer lies in its unparalleled strength and precision. Unlike traditional methods, it minimizes heat distortion, ensures clean welds, and can join even the thinnest materials.
Why Strength Matters in Laser Welding
Strength is critical in laser welding, particularly in industries like aerospace, automotive, and medical devices. A weld’s durability and resistance to stress can determine the safety and longevity of the final product.
If I had to convince you to choose laser welding over traditional methods, I’d highlight its unmatched combination of strength, precision, and efficiency. Whether you’re in aerospace, medical, or automotive manufacturing, laser welding provides the reliability you need to meet industry standards.
How Strong Is Laser Welding?
The strength of laser welding is what sets it apart. From my experience in working with laser technology, I can assure you that its tensile strength often surpasses that of other welding techniques. Imagine creating a weld so durable that it can withstand extreme stress, corrosion, and fatigue — that’s the power of laser welding.
Here’s a breakdown of why laser welds are so robust:
- Tensile Strength: The bonds created through laser welding often exceed the base material’s original strength.
- Corrosion Resistance: The seamless nature of laser welds reduces areas susceptible to environmental degradation.
- Fatigue Resistance: Laser welds maintain durability under repetitive stress.
Key Factors Affecting the Strength of Laser Welding
Material Compatibility and Type
The strength of laser welds largely depends on the materials used. Metals like stainless steel and titanium often yield higher strength due to their ability to withstand extreme temperatures.
Laser Power and Beam Quality
Higher laser power enables deeper penetration, creating stronger welds. Beam quality ensures uniform energy distribution, essential for robust joints.
Welding Speed and Precision
Controlled speed and precision directly impact the weld’s integrity. Faster speeds can reduce heat distortion, while precision ensures defect-free weld zones.
Environmental Factors: Gas and Temperature
Using inert gases like argon prevents oxidation, maintaining weld strength. Temperature control during the process further enhances quality and durability.
Comparison: Laser Welding vs. Traditional Welding Methods
Tensile Strength Comparison
Laser welds often exhibit higher tensile strength compared to TIG or MIG welding, making them ideal for load-bearing applications.
Durability Under Stress
Laser welding ensures uniformity, reducing stress points that could lead to fractures over time.
Resistance to Corrosion and Fatigue
Laser-welded joints resist environmental wear and tear better than traditional welds due to their seamless nature.
What Makes Laser Welding So Strong?
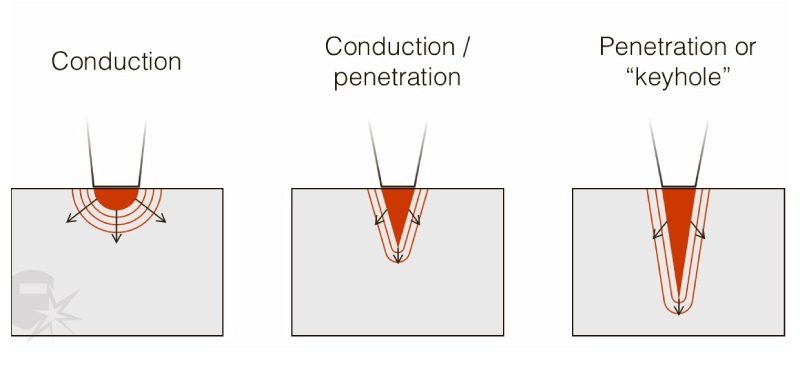
If you’re asking yourself why laser welding outshines other methods in terms of strength, several factors contribute:
Material Compatibility
Not all materials weld equally well, but laser welding excels with metals like stainless steel, aluminum, and titanium. Its ability to create deep, narrow welds makes it perfect for materials requiring high structural integrity.
Precision and Focused Energy
Laser welding’s precision plays a huge role in its strength. Unlike conventional methods, where energy disperses over a larger area, laser welding delivers concentrated energy right where it’s needed. This reduces unnecessary heat, minimizes distortion, and ensures a cleaner weld.
Controlled Heat Input
You probably know how too much heat can weaken a material. With laser welding, you don’t have to worry about this. The controlled heat input ensures the weld retains its original properties, enhancing its strength.
Applications of Laser Welding in Different Industries
Aerospace and Automotive
Laser welding is pivotal in constructing lightweight, durable components, ensuring safety and efficiency in vehicles and aircraft.
Medical Device Manufacturing
The precision of laser welding is unmatched in crafting intricate medical devices, guaranteeing biocompatibility and strength.
Electronics and Microengineering
Micro-welding with lasers allows the creation of compact, robust electronic components essential for modern technology.
Testing and Measuring the Strength of Laser Welds
Destructive Testing Techniques
Techniques like tensile tests assess a weld’s breaking point, providing direct strength evaluations.
Non-Destructive Testing (NDT) Methods
Ultrasound and radiography detect flaws without compromising the weld’s integrity, ensuring reliability.
Analyzing Weld Microstructures
Examining the weld zone’s microstructure reveals details about strength and defect patterns.
Advancements in Laser Welding Technology
Hybrid Laser Welding Techniques
Combining lasers with traditional methods enhances strength and versatility for complex applications.
Real-Time Monitoring and AI Integration
Real-time data ensures consistent quality, while AI predicts and prevents defects.
Future Prospects of Laser Welding
Emerging technologies promise even stronger, faster, and more efficient welding solutions.
FAQ
What makes laser welding so strong?
The precision and controlled heat input create seamless, defect-free joints.
Can laser welding handle high-stress environments?
Yes, it’s ideal for applications demanding superior durability and resistance.
How does laser welding compare to TIG/MIG welding in strength?
Laser welding often surpasses TIG and MIG in tensile strength and corrosion resistance.
What materials benefit most from laser welding?
Stainless steel, aluminum, and titanium excel with laser welding.
Does laser welding compromise flexibility for strength?
No, it balances both, ensuring durable yet adaptable joints.
How can you ensure the strongest welds with laser technology?
Proper material selection, precise laser settings, and thorough testing are key.
How can I maximize weld strength with laser technology?
To achieve the strongest welds, focus on proper material selection, fine-tuning the laser parameters, and ensuring a clean welding environment.
Conclusion
Laser welding is not just a robust joining method—it’s a game-changer in modern manufacturing. Its superior strength, precision, and adaptability make it indispensable across industries. Whether you’re welding intricate microelectronics or large automotive parts, laser welding delivers unmatched performance.