The world of laser welding has undergone a significant transformation in recent years. Gone are the days of bulky equipment and messy processes. Enter laser welding machines – innovative tools that offer unparalleled precision, control, and speed. This game-changing technology has revolutionized fabrication across numerous industries, making how to use a laser welding machine a highly sought-after skill.
Whether you’re a seasoned welder looking to expand your skillset or a complete beginner intrigued by this advanced joining technique, this comprehensive guide will equip you with the knowledge and steps to operate a laser welding machine effectively.
What Is Laser Welding Machine
A laser welding machine is a sophisticated piece of equipment that utilizes a highly concentrated beam of laser light to create strong and precise welds between various materials.
Here’s a closer look at its core components and functionalities:
Key Components of Laser Welding Machine
- Laser Generator: This is the heart of the machine, responsible for generating a powerful, focused laser beam. The specific type of laser used (CO2, Nd:YAG, fiber) depends on factors like the application and the properties of the materials being welded.
- Beam Delivery System: A series of mirrors and lenses precisely direct and focus the laser beam onto the exact location where the weld needs to be created. This system ensures the beam maintains its intensity and delivers the concentrated heat required for welding.
- Control Panel: This user interface allows you to control various parameters crucial for the welding process. These parameters include laser power, welding speed, gas flow rate, and focus settings. Each parameter significantly influences the final weld quality.
- Workstation: This is the designated area where you position and secure the workpieces you intend to weld. The workstation typically incorporates a clamping system to hold the pieces firmly in place during the welding process.
Optional Features: Some advanced laser welding machines might include additional features like:
- Automated Welding Heads: These offer automated control of the laser beam or welding head, allowing for precise and consistent welds even on complex weld paths.
- Fume Extraction Systems: Laser welding can generate fumes, and these systems help evacuate them from the work area, maintaining a cleaner and healthier environment.
- Seam Tracking Systems: These systems use sensors to track the joint seam automatically, ensuring the laser beam stays precisely focused on the weld path, particularly beneficial for long or intricate welds.
How Does Laser Welding Works:
- Laser Beam Generation: The laser generator creates a high-powered laser beam.
- Beam Delivery: Mirrors and lenses within the beam delivery system precisely focus and direct the laser beam towards the desired location on the workpiece.
- Material Melting: The intense heat from the focused laser beam melts the material at the joint where the two pieces meet. Filler material might be added in some cases to create a stronger or wider weld.
- Solidification: Once the laser beam is turned off, the molten material cools and solidifies, forming a strong weld joint.
Advantages of Laser Welding Machines:
- Precision: The small, concentrated nature of the laser beam allows for highly precise welds, ideal for applications requiring tight tolerances and minimal heat impact.
- Cleanliness: Unlike traditional arc welding methods, laser welding is a non-contact process, minimizing spatter and fumes. This translates to a cleaner work environment and less post-welding cleaning.
- Strength: Laser welds can be as strong, or even stronger, than the base materials being joined, making them suitable for high-strength applications in various industries.
- Versatility: Laser welding machines can handle a wide range of materials, thicknesses, and joint configurations. They can even join dissimilar materials that might be difficult for traditional methods.
- Automation: Laser welding machines lend themselves well to automation, making them ideal for high-volume production environments where consistent and repeatable welds are required.
Laser welding machines have revolutionized the joining process across numerous sectors, offering unmatched precision, control, and speed. Their ability to create strong, clean welds makes them a valuable tool for various fabrication applications.
How to Use Laser Welding Machine
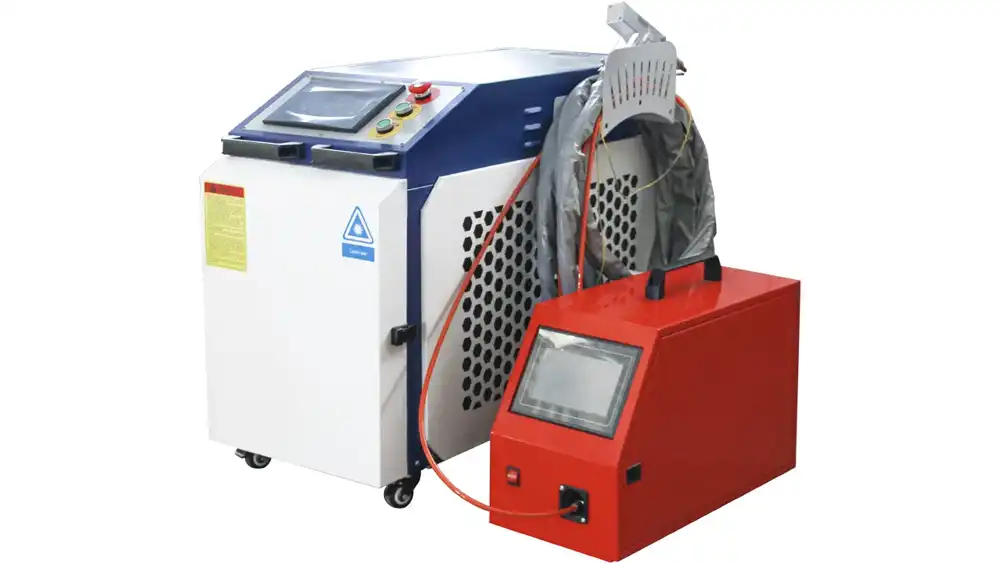
Before We Begin: Safety First!
Laser welding, while incredibly precise, involves concentrated beams of light that can be hazardous if not handled with proper precautions. Here are some essential safety measures to remember:
- Always wear laser safety glasses with the appropriate optical density (OD) rating for the specific laser wavelength used in your machine.
- Operate the machine in a well-ventilated area to avoid inhaling fumes generated during the welding process.
- Ensure the machine is properly grounded to prevent electrical hazards.
- Never look directly into the laser beam, even with safety glasses on.
- Maintain a clean and organized work area to minimize the risk of accidents.
Understanding Your Laser Welding Machine
Laser welding machines come in various configurations and sizes, but they typically share some common components:
- Laser Generator: This is the heart of the machine, generating the high-powered laser beam used for welding.
- Beam Delivery System: A series of mirrors and lenses precisely direct and focus the laser beam onto the desired location.
- Control Panel: This interface allows you to control various parameters like laser power, welding speed, and gas flow.
- Workstation: This is where you position and secure the workpieces to be welded.
- Optional Features: Some machines might include features like automated welding heads, fume extraction systems, and seam tracking systems for enhanced precision.
Familiarize yourself with your specific machine’s manual to understand its components, safety features, and operational procedures.
Preparing for Your First Weld
Now that you’ve grasped the basics and prioritized safety, let’s delve into the steps involved in using a laser welding machine:
Material Selection and Preparation:
- Material Compatibility: Ensure the materials you intend to weld are compatible with laser welding. Some common laser-weldable materials include steel, stainless steel, aluminum, titanium, and various plastics.
- Surface Cleaning: Clean the surfaces to be welded thoroughly, removing any dirt, oil, or contaminants that could hinder a good weld. Degreasers, solvents, or abrasive cleaning methods can be used depending on the material.
- Joint Preparation: Prepare the joint according to the desired weld type. This might involve creating a square butt joint, a lap joint, or a T-joint, depending on your application.
Machine Setup and Parameter Selection:
- Consult the machine manual: For specific instructions on setting up your machine.
- Power Settings: Choose the appropriate laser power based on the material thickness, joint type, and desired weld depth. Start with lower power settings for initial tests and gradually increase if needed.
- Welding Speed: Select a suitable welding speed that balances weld quality with penetration depth. Higher speeds might result in shallower welds, while slower speeds can lead to excessive heat input and potential warping.
- Gas Selection and Flow Rate: Some laser welding processes utilize shielding gas to protect the weld pool from oxidation. The type and flow rate of the gas will depend on the material being welded.
- Focus Adjustment: Fine-tune the laser beam’s focus to achieve the desired spot size and penetration depth. A properly focused beam is crucial for optimal weld quality.
Positioning and Securing Workpieces:
- Proper Positioning: Accurately position the workpieces within the machine’s work area, ensuring the joint is aligned correctly for the desired weld.
- Securing Workpieces: Secure the workpieces firmly using clamps or fixtures to prevent movement during the welding process. Movement can lead to inconsistent weld quality or even weld defects.
Initiating the Weld:
- Double-check all settings and safety measures.
- Activate the laser beam through the machine’s control panel.
- Maintain a steady hand while guiding the laser beam or welding head (depending on your machine setup) along the joint to be welded.
Post-Weld Procedures:
- Allow the weld to cool completely before handling or manipulating the workpieces. Once the weld has cooled, you can proceed with post-weld procedures:
- Visual Inspection: Carefully inspect the weld for any cracks, porosity, or other defects. Visual inspection is the initial step to assess the weld quality.
- Deslagging (if applicable): Some materials, like stainless steel, may have a thin oxide layer on the weld pool. This layer, called slag, needs to be removed using a chipping hammer or wire brush to ensure a clean and smooth weld finish.
- Grinding and Finishing (optional): Depending on your application, you might need to grind or polish the weld for aesthetic purposes or to achieve a desired surface finish.
Tips and Techniques for Effective Laser Welding:
- Practice on scrap material: Before attempting welds on your actual project, practice on scrap pieces of the same material to get comfortable with the machine settings and develop your hand-eye coordination.
- Start with simple welds: Begin with simple butt joint welds on thin materials before progressing to more complex joint configurations or thicker materials.
- Experiment with settings: Once you’ve grasped the basics, experiment with different laser power, welding speed, and focus settings to understand their impact on the weld quality. However, make adjustments gradually and consult the machine manual for recommended parameter ranges.
- Maintain a clean work environment: A clean work area free of debris and contaminants helps ensure consistent weld quality and minimizes the risk of spatter or fume buildup within the machine.
- Keep your laser welding machine well-maintained: Regularly clean the lenses and mirrors in the beam delivery system to maintain optimal laser beam quality. Schedule periodic maintenance checks as recommended by the machine manufacturer.
Advanced Laser Welding Techniques:
As you gain experience with laser welding, you can explore more advanced techniques to expand your capabilities:
- Seam Tracking: Some laser welding machines incorporate seam tracking systems that use sensors to follow the joint automatically. This is particularly beneficial for long, intricate welds or situations where maintaining a perfectly straight line manually might be challenging.
- Pulse Welding: This technique involves delivering the laser energy in short pulses rather than a continuous beam. It offers greater control over heat input and can be beneficial for welding thin materials or minimizing heat distortion.
- Deep Penetration Welding: By adjusting parameters and potentially utilizing specific welding heads, laser welding can achieve deep penetration welds suitable for joining thicker materials.
Laser Welding Machine Applications

Laser welding machines are finding uses in a wide range of industries due to their versatility and precision. Here are some of the most common applications of laser welding machines:
- Automotive Industry: Laser welding is extensively used in the automotive industry for joining thin, high-strength steels in car bodies, chassis components, complex engine parts, and even battery packs for electric vehicles.
- Medical Devices: In the medical device field, laser welding is crucial for creating hermetic seals for pacemakers and other implantable devices, along with fabricating delicate surgical instruments. The clean and precise welds ensure sterility and functionality of these vital medical tools.
- Aerospace: The aerospace industry relies on laser welding for welding high-performance metals like titanium alloys for strong, lightweight aircraft structures. Laser welding also plays a role in repairing turbine blades, extending their lifespan and ensuring the safety of aircraft.
- Electronics Manufacturing: Miniaturization and high-density packaging are key trends in electronics manufacturing. Laser welding machines offer the precision needed to precisely join tiny electrical components on circuit boards.
Conclusion: Quote Laser Welding Machine for Your Project
By following these steps, familiarizing yourself with safety procedures, and continuously honing your skills, you’ll be well on your way to mastering the art of laser welding. This versatile technology offers a unique combination of precision, control, and speed, making it an invaluable tool for various fabrication applications.
Ready to unlock the potential of laser welding in your own projects?
Explore the wide range of laser welding machines available, and choose the one that best suits your needs and budget. With the right equipment and knowledge, you can achieve high-quality, precise welds for a wide variety of materials.